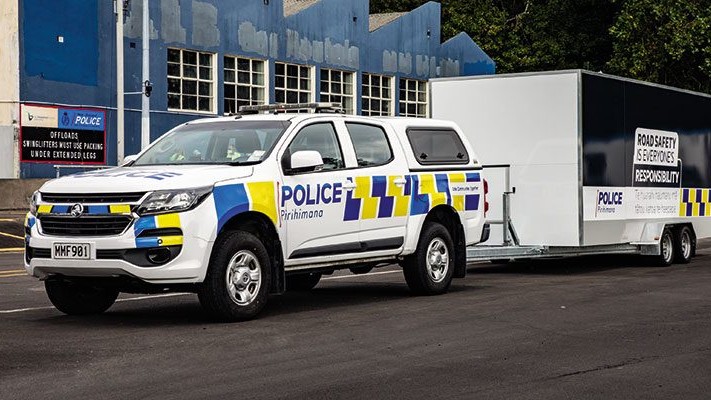
The NZ Police in conjunction with the Waka Kotahi NZ Transport Agency have commissioned six mobile roller brake test units. Before they were deployed nationwide, we went to a demonstration day to see what’s about to pop up on a roadside near you! And why.
Representatives from the Police Commercial Vehicle Safety Team (CVST), Waka Kotahi NZ Transport Agency, National Road Carriers, Ia Ara Aotearoa Transporting New Zealand and the industry were among the guests at the recent demonstration of a mobile roller brake test unit held at the Stanley Street Commercial Vehicle Safety Centre in Auckland. It’s the first of six units being deployed nationwide by the police, to be operated by the CVST.
In partnership with other agencies and industry, the roller brake test machines will complement Waka Kotahi NZ Transport Agency’s Weigh Rite programme and assist in achieving the standards required in the Road to Zero programme, part of which includes safety standards of the nation’s vehicle fleet.
“This is a prevention tool first and foremost,” said acting inspector Lex Soepnel. “It’s about preventing accidents before they happen. It also means we can cover the entire country. They can be deployed anytime, anywhere. A unit will be assigned to each of the four CVST regions, and two will float.
“Up until now, the only roller brake tester we [the CVST] have had is the one in the Paengaroa Commercial Vehicle Safety Centre in the Bay of Plenty. These will change that significantly. Now it doesn’t matter where you are, they could pop up.”
Soepnel pointed out how important it was to improve the testing network, saying that even though local operators knew the Paengaroa centre was there, of 2500 trucks tested between 2018 and 2021, 67% failed the roller brake test.
“It’s not the first time we’ve used a mobile roller brake tester roadside. We had a set in the mid-1990s, but they weren’t successful. These new ones are incomparable. Aside from technology advancing, we’ve overseen and been involved in the specification and build all the way through. They’re spec’d and built for our needs, to suit our operations, and conditions in New Zealand.”
The rigs
The mobile roller brake testing machines and rigs were sourced from BM Autoteknik in Denmark and supplied through Sulco Tools & Equipment in New Zealand. Equipment manager for Sulco, Brett Higgins, will be well known to many readers, with 38 years’ experience in the field. Brett headed the project from the supplier end and, as part of the wider deliverable, he also oversaw the build and set-up of the New Zealand-made Pinto trailers used to transport the roller brake testers and associated equipment.
Each unit weighs about three tonnes and comprises the roller brake tester, ramps, an electric winch for deployment and recovery – with a hand winch as a failsafe – trolley jack for setting up, petrol generator, laptop computer, wireless tablet, calibration kit, cones, and everything else needed to operate autonomously. Set-up time from go, to the first wheels on the rollers, is about 22 minutes.
The mobile roller brake testers
“Roller brake testers are not new in New Zealand – the first ones were deployed in 1995,” said Brett. “The 2006 Heavy Vehicle Brake Rule requiring COF brake testing at 60% of axle-design weight had a significant impact on roller brake tester numbers used in the heavy transport sector here and, today, there are more than 800 roller brake testers in operation nationally for both the truck and car industry sectors. The BM Autoteknik brand is the most installed roller brake tester in New Zealand and is an industry- leading marque in its homeland and throughout Scandinavia and Europe where it’s used in both commercial, inspection stations and policing applications.”
The BM20200 model mobile roller brake tester is configured to operate identically as the vehicle testing stations but in mobile form. The main point of operational difference is the speed of the rollers. Because they’re not mounted in-ground, they turn much slower. This, according to Brett, has no impact on accuracy or repeatability.
Modifications to these New Zealand field units ex-the manufacturer were primarily larger wheels to make them easier to move around roadside, a deadman’s instant cut-off switch, and longer platforms on either side of the rollers so the entire axle-group being weighed could be accommodated at a uniform height.
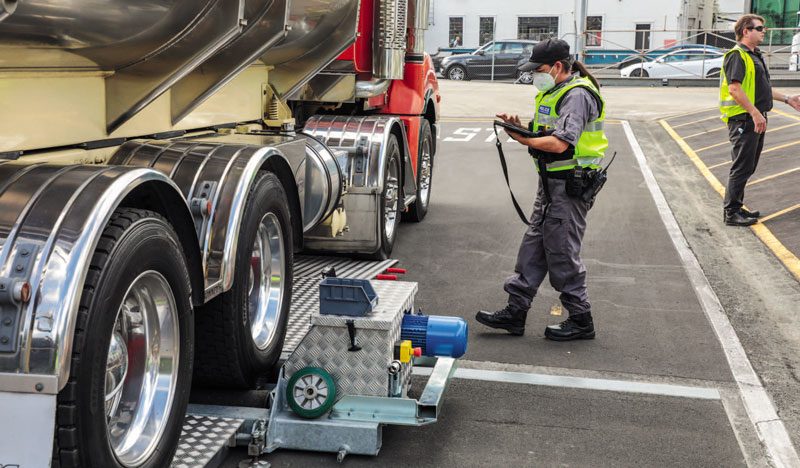
Calibration occurs every 12 months, although each unit carries a calibration kit if a certified tech needs to visit them in the field.
The unit does not have to be on level ground to work (the road is rarely level, after all), but it can’t be twisted. To combat any risk of twist, it sits on six adjustable feet that also double as the weight load- cell measure points. The roller bed has a smaller central roller, there to measure wheel speed. It stops the test rollers the instant it detects lock-up, preventing any possibility of damage to tyres. The unit can test axles up to 16 tonnes in weight, in -30C°, so New Zealand conditions will generally fall well within its working envelope. The brake rollers have been designed with a surface friction co-efficient that matches New Zealand roads.
“Essentially, we’re looking at a giant torque gauge,” said Brett. “Brake force divided by axle weight equals efficiency.” Brake tests can be performed for service brake and park brake on the left and right sides of an axle independently. The unit can test drum or disc brakes; air or other mechanical park brake systems. Whether an axle is mechanically or air-suspended is of no consequence.
“Although able to accommodate pull-down testing, there has been a procedural decision around officer safety not to do so roadside.”
LW Bonney and Sons supplied the test truck. Testing took about 15 to 30 seconds per axle. The readout appears on the central PC in the trailer, relayed out to the wireless hand-held tablet with the VSO (Vehicle Safety Officer) truck-side. The results can then be monitored and discussed with the driver.
“Does it have even brakes? Are they in balance? These are the two questions the officer is seeking answers to,” Brett said. “The pass criteria for service brake efficiency is over 50% for each axle. In terms of brake imbalance between left versus the right side of an axle, a 30% or worse imbalance will mean pulling to the left or right under braking.”
The key to an accurate reading is slowing the speed of brake application. A gradual increase in pressure on the brake foot pedal is key to getting the best results. “Stabbing or stomping your foot on the brake results in a non test,” said Brett. At the end of the testing, the driver can take a printout away if they request it.
“The question of brake temperature at the time of test often arises,” said Brett. “As does the dynamic weight versus static or presented weight. Both are inconsequential in terms of the maths and the numbers recorded impacting the overall outcome. As we always say, ‘when a kid rides out in front of you when your brakes are cold, you’ll still need them to work’.
“When a truck is requested to stop, the VSO enters the registration, configuration, and the number of axles and they’re away.” The database of trucks amassed on the day of testing is autonomous, i.e. not feeding live into a national database at the time.