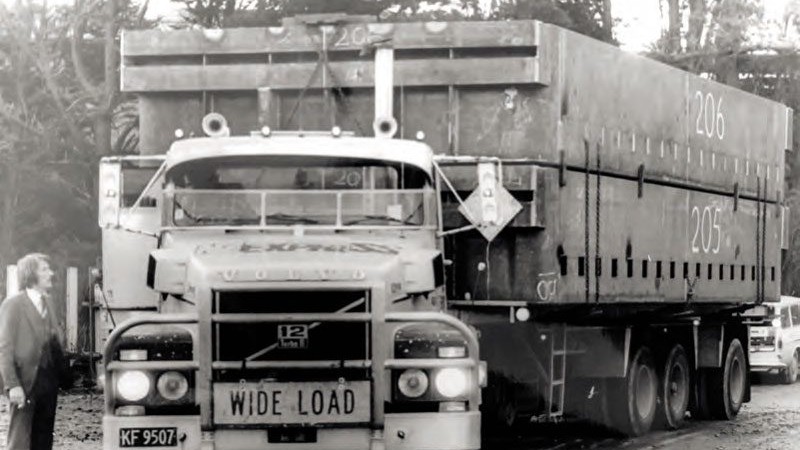
The expansion of the Tiwai Point aluminium smelter in the early 1980s called for innovative engineering and transport. As always, Kiwis were up to the job, none more so than the team at NZ Express Transport in Christchurch. Forty years on, even with today’s equipment, achieving the same result would be just as impressive.
New Zealand Aluminium Smelters at Tiwai Point, Bluff, decided to increase production of high- grade aluminium in the early 1980s by installing a third pot line. The new line would be housed in a building 600m long and contain 208 cathode pots.
The National government of the day, led by Prime Minister Rob Muldoon, supported this decision, and it ended up part of the massive fiscal policy programme of the era known as Think Big.
In late 1980, tenders were called to construct the additional pot line over two years, starting in 1981.
Andersons Foundry in Christchurch won the contract to manufacture the cathode pots and related steelwork, while CWF Hamilton & Co, also in Christchurch, won the contract to make the anode and cathode buzz bars.
Tenders then went out to transport all manufactured components for the smelter from Christchurch to Tiwai Point. NZ Express Transport Christchurch (NZE) was awarded the contract.
Each cathode pot was 9.6m long, 3.8m wide, and 1.2m high. They were made from 25mm and 30mm plate steel and weighed 9.4 tonnes each.
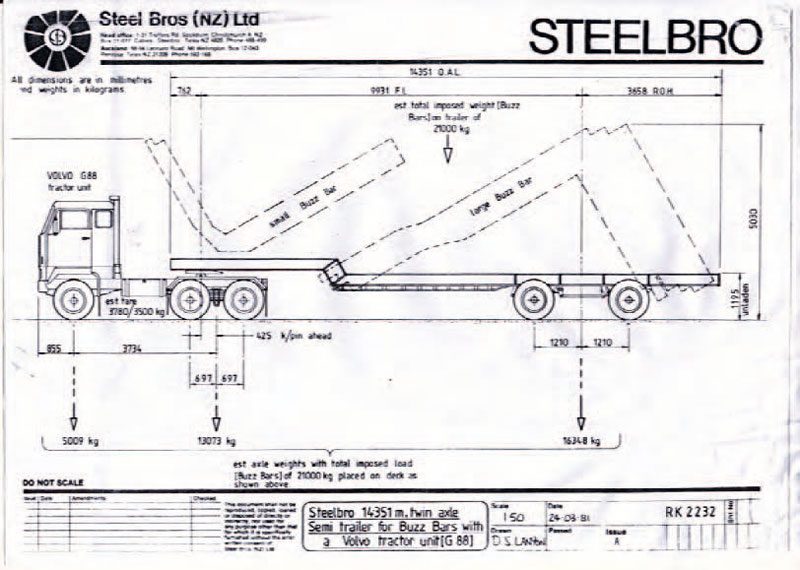
NZ Express designed and made special ‘H’-shaped yokes that were spaced at four intervals along the top side of each bottom pot, with the second pot located and loaded onto the H yolk. The load was then secured in preparation for the 615km journey south to Tiwai Point.
Jigs were attached at each end of the pots for both loading and unloading, and these were also used for load security when securing the load to the semi-trailer.
On 17 August 1981, the first of 104 loads left Christchurch for Tiwai Point.
The steelwork associated with the pots comprised 208 deck plates, each one 10.8m long, 4.3m wide, 25mm thick, and weighing three tonnes.
These were carted six at a time on two jigs manufactured from 150mm x 150mm RHS, 4.3m in length, with an internal upright at each end. Using strengthened semi-trailers, they secured onto twist locks, and during loading, the uprights guided each deck plate onto the jigs. The six plates were then uniformly positioned for the journey, overhanging the semi-trailers on each side.
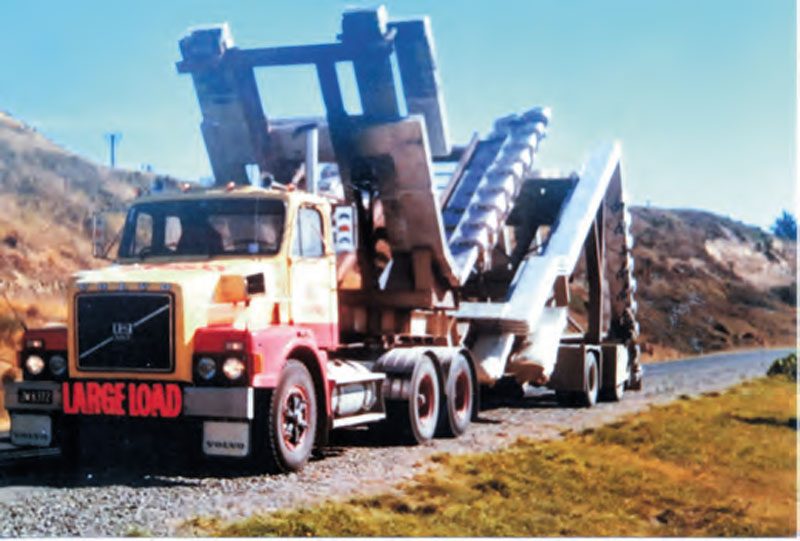
The transport of the deck plates began on 17 September 1981, concluding 12 months and 35 loads later.
Considering the work ahead of them, NZE purchased two new Volvo N12 tractor units, operated by Pat Shields and Murray Glen. A Volvo N10 tractor unit in the care of Graham Forbes was also on hand to help out, along with other existing trucks from the fleet that included a Volvo G88 driven by Dick Horgen and a Hino HH V8 with either Trevor McLintock or Grenville Beri behind the wheel.
The Murray Glen machine was changed over to the CWF Hamilton buzz bar work two months later once that production had started.
Every load required a Class II pilot. NZE staff of the time Jim Carey, Ian White, Stu Ford, Bill Salt, Reade Cassin, Phil Timehau and Ken McQuilken, were joined by general manager Peter Boyd, operations manager Kevin Richards, and transport manager Geoff Carpenter, to to fulfil this requirement.
During one of the loads, an overzealous Dunedin- based traffic cop stopped the convoy and measured things up. He declared the load was over width by the diameter of the chain securing it, and each load would require the ‘assistance’ of a full MoT escort from then on. Obviously, this additional cost had not been budgeted for, so the next load that went down was piloted by Peter Boyd, who “sorted the cop and the situation out”.
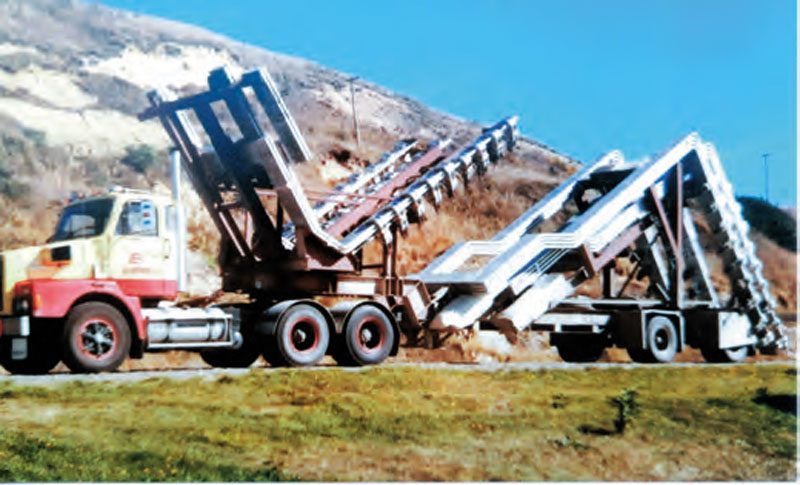
During this time, with so many staff and units from the Christchurch fleet out of town, local jobs started piling up, causing stress and anxiety to the rest of the local dispatch team. However, as it was in the day, everybody pulled together to ensure things were kept running smoothly from the customers’ point of view. Evidently, the old analogy of a duck looking calm on the surface but paddling furiously underneath was the best way to describe it.
Along with the NZE trucks carrying the components south, NZ Railways was also roped in to help. They carried a total of 3744 cradles, each measuring 4.8m long, 1.6m high and 0.25m wide, weighing in at 911kg. The cradles were carried on UN type railway wagons and loaded at the Andersons Foundry siding by NZE staff. Once the wagons got to Invercargill, they were unloaded by Southland Freight Haulage operations manager John King, after which the cradles were then trucked 27km to Tiwai Point. Maximum loading on the railway wagons was achieved by inverting two rows of cradles onto the uprights of the lower ones, which meant each wagon carried 45 cradles weighing a total of 41 tonnes.
John King was also great at finding backloads to Christchurch for the NZE trucks.
Each of the cathode pots positioned at the smelter is supported by 18 cradles with each deck plate bolted onto the cradle tops. The cathode buzzbars were manufactured from 99.98% pure aluminium billet railed from Invercargill to the CWF Hamilton & Co rail siding in Christchurch. The metal was pure and therefore very soft and could easily be damaged during transportation.
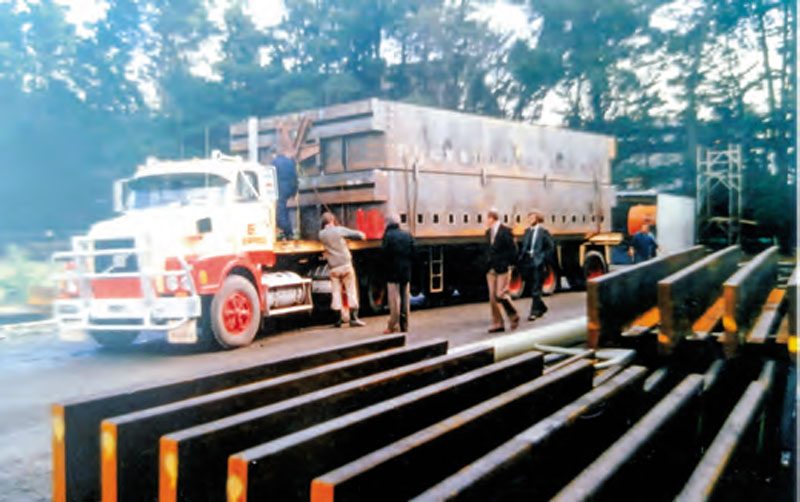
Steel Bros of Christchurch was employed to design and build two dedicated semi- trailers for this job (see the attached plan for the trailer). The semis were essentially a chassis with support frames to load the buzzbars onto. Staff from CWF Hamilton & Co loaded and secured the loads, and while one trailer was being unloaded at Tiwai, the second trailer was being loaded in Christchurch. The loaded dimensions of these units were 3.0m wide, 4.8m high, and weighed 22.7 tonnes each. The loaded height of 4.8m was the maximum that could pass under Watermans Bridge on the Dunedin motorway. Even so, the rear buzzbars had to overhang, allowing it to sit lower than the semi-trailer chassis.
This work commenced on 25 November 1981 and ran through to 18 November 1982. There were 104 of these loads in total, all completed without incident by Murray Glen in his Volvo N12.
It is a historical account of Kiwi can-do and innovation at its finest. Recollections of the mood and atmosphere in and around the contract also reflect the true camaraderie of the era. During the time, several NZE Christchurch staff stayed at Invercargill’s Coachman Inn three nights a week for 15 months. Rumour has it there were a few big nights at the bar.
Of course, the lessons and experience gained from completing jobs like this result in improved capability. In the years following, NZ Express Transport Christchurch won many other specialised jobs.
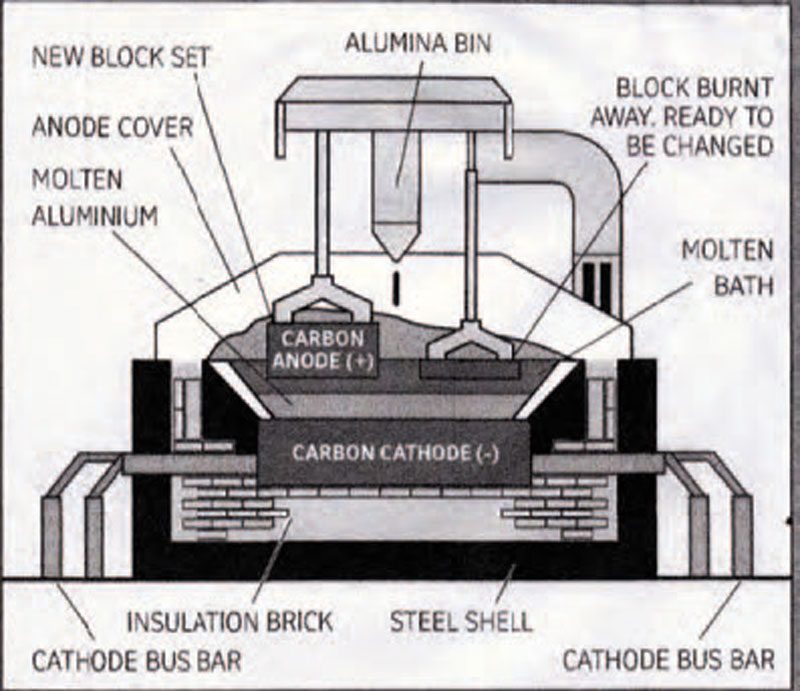
FRYING SAUCERS!
New Zealand Aluminium Smelters (NZAS) owns and operates the country’s only aluminium smelter at Tiawai Point near Bluff. It is a joint venture operation between Rio-Tinto and Sumitomo Chemical Company of Japan.
The smelter began operations in 1971 and produces 360,000 tonnes of aluminium annually. Of this, 90% goes to export, with the largest market being Japan.
Tiwai Point was identified in the 1960s as the location for the smelter as it met some key prerequisites. One, there was the availability of continuous hydroelectricity from Manapouri Power station. Two, a deep-water harbour. Three, support services close by in Invercargill. Four, favourable environmental and climatic conditions.
Bauxite ore is mined at Weipa on the Cape York Peninsula in Northern Queensland and shipped to Gladstone in Central Queensland for refining into fine white alumina powder. The alumina is shipped to Tiwai, where aluminium is produced. Four tonnes of Bauxite produce two tonnes of alumina powder, which produces one tonne of aluminium.
To produce aluminium, 196,000 amps of current pass through the carbon anode blocks to the cathodes at the bottom of each pot. The pots are lined with special refractory bricks from Europe that are able to withstand operating temperatures of approximately 930°C.
The molten metal is tipped into holding furnaces and heated to 730°C, considered the best casting temperature, for pouring into ingots, extrusion billet, rolling block, or ‘T’-bar.