Hydrogen gets heavy
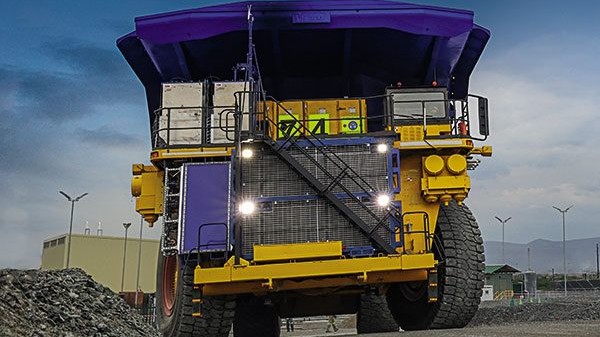
Mining giant Anglo American has unveiled a prototype of the world’s largest hydrogen-powered mine-haul truck as part of its nuGen Zero Emission Haulage Solution (ZEHS).
In December 2019, Anglo American signed an agreement with the United States engineering company, First Mode, to design the world’s largest fuel-cell electric vehicle (FCEV). After a robust testing process, a plan would exchange the current heavy-haul fleet’s diesel ICE-power system with a hybrid hydrogen fuel-cell and battery powerplant. The model chosen for the exchange was the Komatsu 930E-4 Ultra Class haul truck with a 2700hp diesel engine connected to an alternator at Anglo American’s Mogalakwena Platinum Group Metals (PGM) mine in South Africa.
The converted truck, designed to operate in everyday mining conditions, is part of Anglo American’s nuGen Zero Emission Haulage Solution (ZEHS). nuGen provides a fully integrated green hydrogen system of production, fuelling and haulage, with green hydrogen to be produced at the mine site.
nuGen is part of FutureSmart Mining, Anglo American’s innovation-led approach to sustainable mining that brings together technology and digitalisation to drive sustainability outcomes, including its commitment to carbon neutrality across its operations by 2040. Diesel emissions from Anglo American’s haul-truck fleet account for 10-15% of its total Scope 1 emissions, with about 16% of the Scope 1 emissions from the direct use of diesel in mining and processing. There are more than 400 heavy-haul trucks within its worldwide operations, each typically burns 2500L to 3000L of diesel and generates eight tonnes of CO 2 per day (900,000L per year).
“Over the next several years, we envisage converting or replacing of our current fleet of diesel-powered trucks with this zero-emission haulage system, fuelled with green hydrogen. If this pilot is successful, we could remove up to 80% of diesel emissions at our open-pit mines by rolling this technology across our global fleet,” says Duncan Wanblad, chief executive of Anglo American.
For the nuGen project, Anglo American worked with some of the world’s leading creative engineering and technology companies, such as ENGIE, First Mode, Ballard and NPROXX. The partners developed the fuel-cell battery system and drivetrain as well as the software solution that manages the power and energy between them. And it was a significant undertaking – nothing on this scale had ever been built, and a key challenge was to retrofit an entirely new power system into a space formerly occupied by the diesel powerplant while continuing to support all the auxiliary systems of the truck. The truck has eight fuel cells, with a collective capacity of 837kW, and a 1.2MWh lithium-ion battery pack. These allow it to generate a staggering 2MW of power. It’s capable of carrying a 290-tonne payload, and with a tare weight of 220 tonnes, it tips the scales at 510 tonnes fully laden.
In parallel, Engie, a French multinational specialising in energy transition, provided an integrated hydrogen solution for the Mogalakwena Mine that could produce, compress and store hydrogen on site and enable the trucks to be refuelled in record time. Critical to the project was that the hydrogen would be generated as far as possible using local solar energy, maximising the amount of ‘green’ hydrogen used to fuel the truck. A 100MW solar photovoltaic plant is under construction, due to enter service by the end of 2024. The site incorporates the largest electrolyser in Africa, which will be able to generate and store an estimated one tonne per day of hydrogen to refuel the trucks.
At its official launch last year, the nuGen hybrid hydrogen-battery power system performed faultlessly, demonstrating its ability to improve overall efficiency by recovering energy through regenerative braking.
Anglo American plans to retrofit 40 diesel haul trucks at Mogalakwena with hydrogen power, before rolling out the technology across its global fleet of about 400 trucks at seven open-pit mine sites by 2030.
Read more
Stars with the X-factor
0 Comments8 Minutes
Next-level electric
0 Comments12 Minutes
Hamish Dalziell
0 Comments4 Minutes