IRTENZ Conference 2023
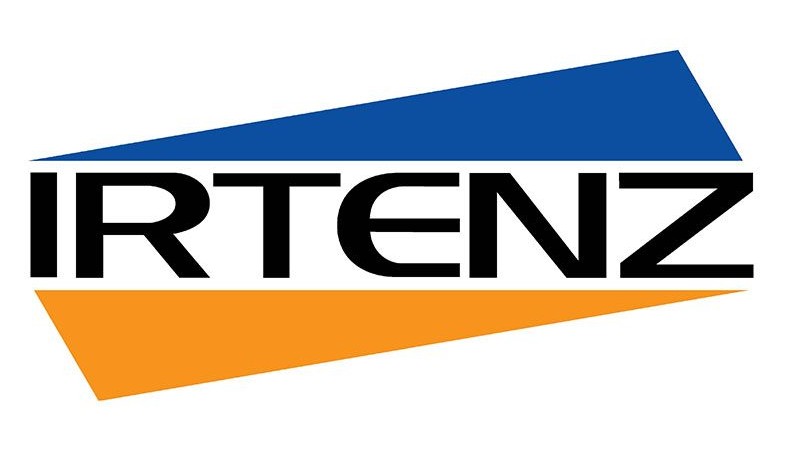
Technology, productivity, labour and education were among the many topics discussed at the IRTENZ 18th international conference, themed Future Highways – Future Vehicles, in mid-November. As always, the conference gathered some of the brightest local and international minds, driving vehicle and infrastructural engineering for the transport industry. We’ll cover some of the presentations and discussions in coming issues. This month, infrastructure and enforcement.
Opening the conference, IRTENZ president Chris Carr remarked, “there’s an awful lot coming towards us…” That certainly set the tone for the 2.5-day conference, as 23 individual sessions were needed to cover the presentations, which addressed infrastructure and enforcement, labour and skills, performance-based standards (PBS) and future vehicles.
“Productivity remains important, but it’s going to come under pressure. The population is increasing, and our demand for goods and services is not going to decrease. All while we remain hampered by our geographic position,” Carr said.
“Meanwhile, in February, we discovered the word ‘resilience’ – at some point, someone forgot about the black stuff we drive on… Waka Kotahi is going to have to take a more cooperative approach as these problems come to a head, including how we deal with heavier vehicles [as the likes of electric trucks become more commonplace] and higher lengths and dimensions.”
In his keynote address, IRTENZ’s past president, Dom Kalasih, commented that many of the really hard challenges were still coming. “Decarbonisation is a request that we re-industrialise – it’s a change of that level of significance,” he said.
“It is incumbent on our sector to continue advocating a sensible way forward and shift the increasing risk and demands on operators. At the moment, most of the focus on decarbonisation is put on operators, regulators and OEMs – that’s risky, decisions need to be made at a much higher level. As long as road control authorities are mucking around in the weeds, the meaningful conversations are never going to happen.
“Transport operators can do anything so long as it makes commercial sense, and a lot of the enabling technology is there now, but we can’t do it alone.”
Carr continued: “We have to be more open with our data, have to be part of giving the regulators and road authorities our info, and that’ll be pretty painful.
“There has to be an improved level of trust because the less damage the roads suffer, the more we can use them and unlock productivity.”
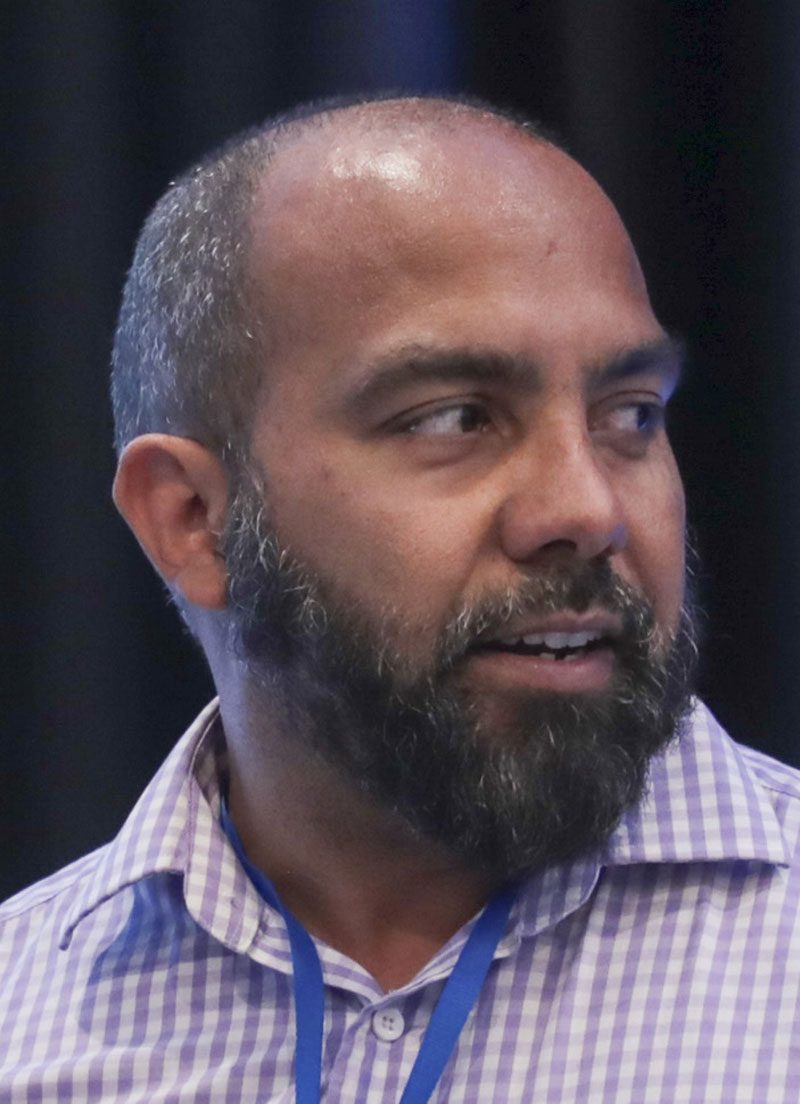
Vehicles and infrastructure
First up, Riccardo Areosa, safer commercial transport programme manager, began with a nod to some of the successes borne from the refreshed PBS standards in 2019 (which included a width increase to 2.55m from 2.5m and a height increase to 4.3m from 4.25m). These included the 29m B-train for the Port of Napier (New Zealand Trucking, October 2019), and recovery units for disabled combinations. “PBS testing was undertaken with Ace Heavy Towing to determine a framework of operation and a permitting regime to allow that vehicle to tow combinations. There are six heavy-tow vehicles of this nature around the country now.”
Areosa commented that ‘green trucks’ were the next challenge. “The barriers are that they are heavier, carrying extra weight for the battery, with reduced payloads, and have heavier axle loading.
“We’re waiting to see which way we go in terms of infrastructure, but we know there are limitations, and we are actively working with industry to test them and see what the future may look like.”
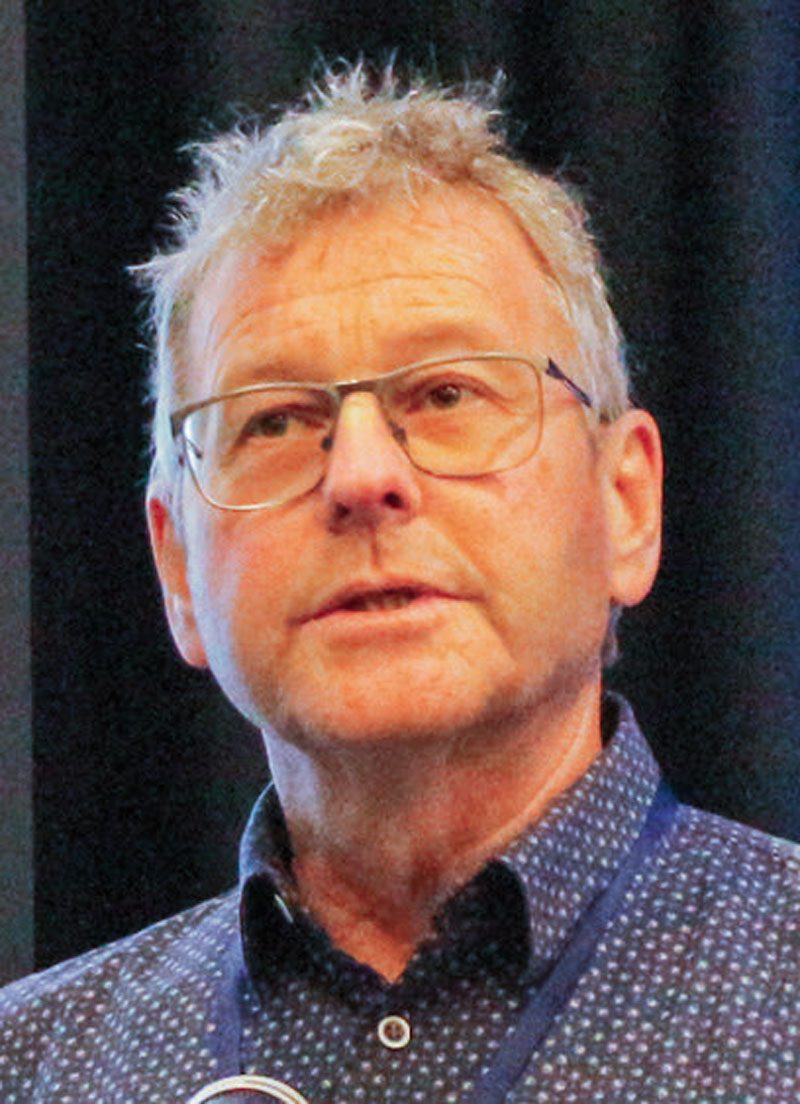
Peter Brown, maintenance and operations regional manager, West Coast, Canterbury, Otago and Southland, discussed the impact of road freight on road assets and what the agency needs to do to accommodate heavier vehicles in the future.
He said climate change was happening and decarbonisation was needed, which meant heavier [zero emission] vehicles. In addition, the road freight task was increasing and productivity demanded heavier loads. This was problematic for the road network.
“New Zealand’s road network is fragile. It has unique geological and drainage issues, especially in the North Island. To counter that, most of the network is built with flexible and granular pavement. The pavement, under surface level, is the key – it takes the load.”
He said HPMVs were introduced in 2014 when the government decided to ‘sweat the asset’. “Maintenance and renewals were underdelivered in 2022/2023 and in previous years.” The cost of maintenance and renewals was escalating exponentially, he said, adding that limited contractor capacity stemmed from the government turning off the tap in 2014, causing skills and capability to leave the industry.
“The DTIMS infrastructure management system tells us 10% of our network is ‘broken’, meaning it needs to be rebuilt,” he said. Brown said there were 10 years’ worth of work to return the full state highway network to acceptable levels.
“Road rehabilitation has become a core part of our renewal programme. We should be doing 450km to 500km of rehab every year … currently, we’re only doing 150km. By the end of 2033, we’ll be at 2% of the whole state highway network. However, from now on, we are ramping up to 600km a year by 2026/2027. This means the funding need increases significantly, needing around an extra $500 million per annum.”
Alarmingly, Brown said all this only returned the network to 2014 levels, and the road network needed to be brought to a level that would align with today’s freight task. In the meantime, future needs must be accounted for.
“If we [Waka Kotahi] accept that vehicles and freight loads will get heavier, these increased loads will ‘consume’ the life of our pavements faster. That means our state highways will have to be strengthened.”
To achieve this, Brown said future road treatments would need to utilise modified pavements – using less chip-seal and engineering deeper pavements with more foam bitumen and more structural asphalt. He added that more drainage was needed in the interim to keep existing pavements as strong as possible.
Brown commented that the network’s thousands of bridges were its greatest limitation. “Our bridge stock is quite old [especially on local roads], and the majority of structures will need to be strengthened.
“In addition, future roads will require better draining maintenance and improved alignments for potentially longer trucks. All this adds to the cost of upgrading the network for future loads,” Brown said.
In looking to a future network, Brown said thinking needed to change. “There’s a significant up-front cost to building a stronger network. Funders are always sensitive to current costs because of competing requests. The real shift needs to be in how we think about that asset. We’re engaging with funders on whole-of- life costs. Stronger roads would be more expensive but have a longer service life and require less maintenance over time. Less maintenance and better conditions mean less disruption to road users, and also equals a carbon reduction.”
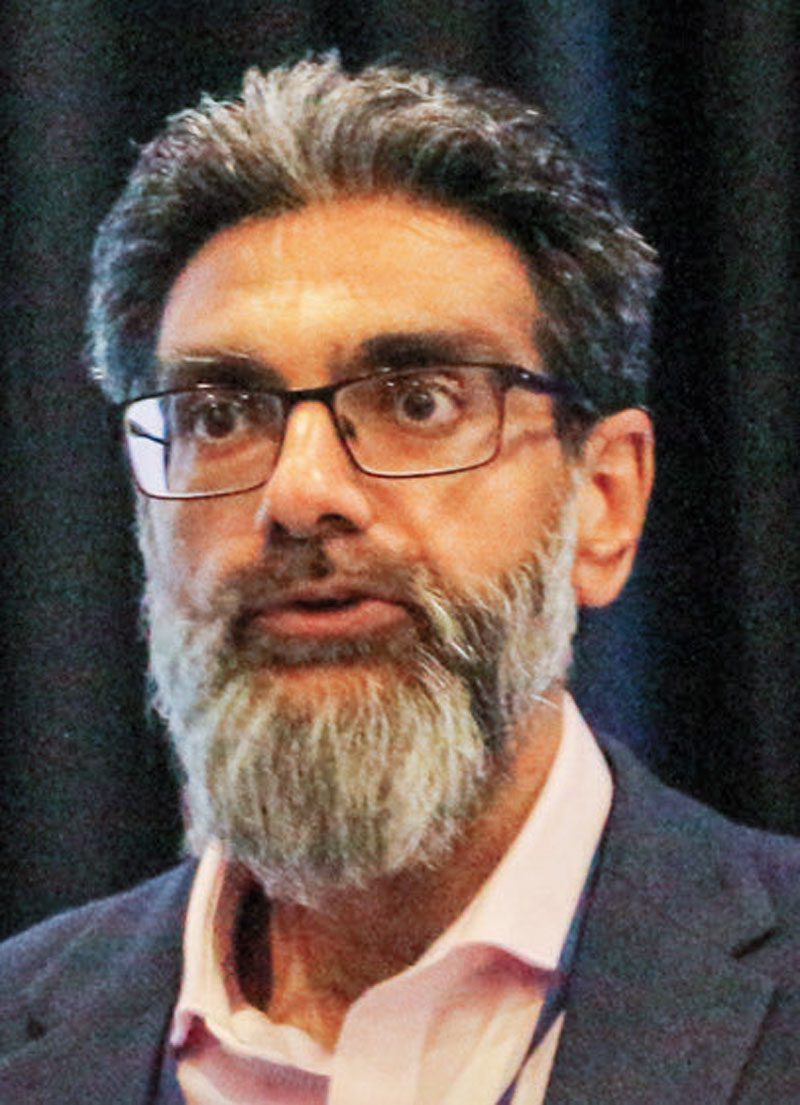
Tariq Ashraf, principal planning advisor at Waka Kotahi, touched on opportunities and challenges for managing New Zealand’s evolving urban freight task.
“Land transport is fundamental for our liveability; it’s an important economic sector. The total freight task is 278,800,000 tonnes and 30.1 billion tonne/km, and road accounts for 93% and 71% of those figures.”
Ashraf said 67% of road freight travelled less than 100km, 16% 100km to 200km, 6% 200km to 300km and 16% more than 300km.
“Forecasts show a 39% increase in total freight volume by 2052, driven by demand-driven commodities (growing by 56% over the next 30 years), increasing population and consumer expectation,” he said, indicating this would add tremendously to the 67% urban road freight movements.
He said there were five considerations for optimising urban freight movements of heavy vehicles:
1) A strategic freight network – This included identifying and prioritising the most critical parts of the land transport network for responses. Some strategic networks in major cities were overburdened, underdeveloped and inefficient.
“It needs to be high performing, working as a system to move large volumes of freight. Identifying a strategic network is a necessary first step but insufficient on its own. Past efforts to improve network performance by increasing capacity on the strategic network have been less effective than hoped,” he commented.
2) Network optimisation – This included maximising the use of the existing network to create extra road capacity; small physical interventions, active network management, road space reallocation, behaviour change and technology (signal optimisation) and freight lanes (including investment in new capacity where required).
“We can enable quicker journeys along key freight routes during inter-peak periods, and more reliable journeys during peaks by managing congestion.”
3) Urban form. “Mixed-use development will put pressure on our freight and supply chain system and urban networks,” Ashraf said. The right balance for the movement of people and goods through integrated land use and transport planning was needed. The distance goods needed to be moved between homes, workplaces, distribution centres and ports needed to be optimised. “And this has to recognise the value of freight to society.”
4) Intermodal freight terminals – These can provide efficient and effective freight transfers between different modes, improve productivity and reduce negative effects from freight movement. “A mode shift from road to rail and coastal shipping could increase the need,” he added.
5) Road/congestion pricing – To optimise network use and protect the transport network for the highest priority uses. It’s being considered for Auckland and is available as a tool, subject to legislation.
“We will continue to work with councils on urban/spatial plans and transport plans and work with the Ministry of Transport and industry to support the removal of barriers to innovations. Collaboration with industry will allow us to gain better data to trial potential solutions,” he concluded.
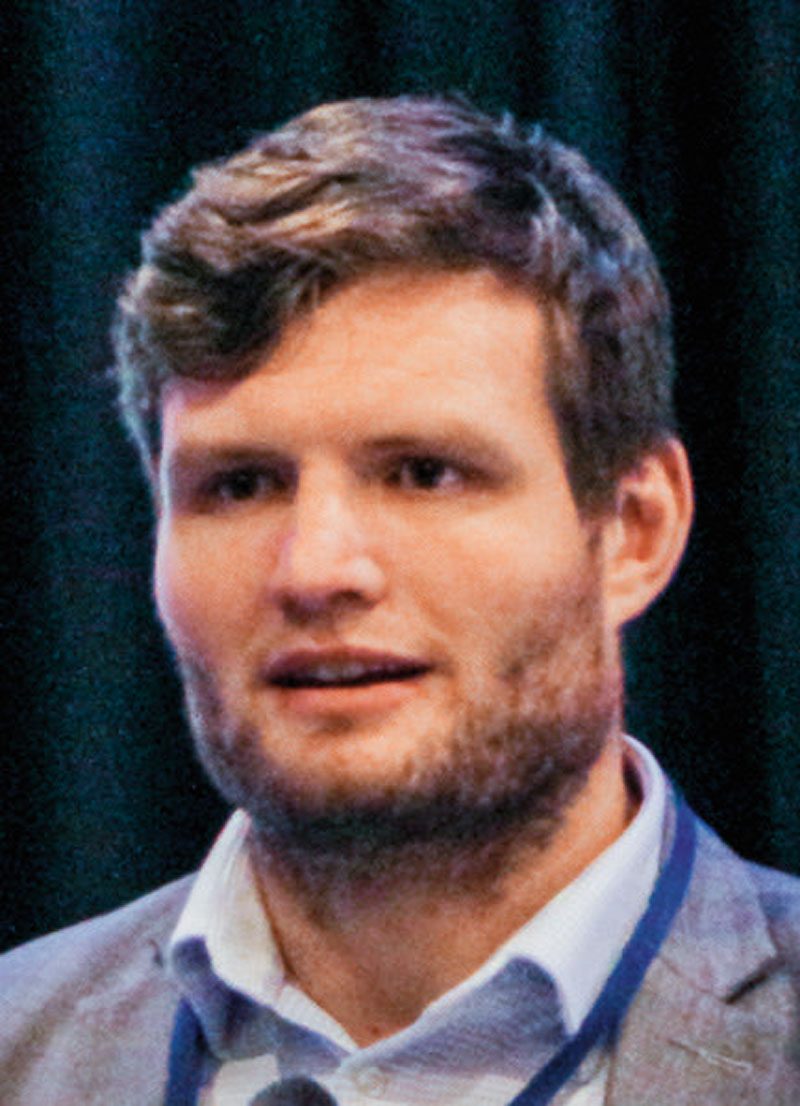
Commercial vehicle safety and enforcement
Sean Bridge, commercial vehicle safety programme (CVSP) manager at Waka Kotahi, discussed the potential impacts of new technology vehicles on the commercial vehicle safety programme. He said there were currently more than 150 weigh pits across the country, and vehicles were randomly selected for inspection when these were operational. This only provided a single point of data intelligence at a point in time. In addition, there was limited capability or capacity to regulate the number of active TSLs and heavy vehicles on our roads.
“We are moving considerably from weight screening at weigh pits towards risk targeting and allowing compliant operators to continue their journeys,” Bridge said. In doing so, the agency has funded 12 new commercial vehicle safety centres (CVSCs) that will cover 46% of heavy vehicle kilometres, with planning to fund an additional 22, improving that figure to 76%.
“We want to build a picture of our operators from millions of data points. The CVSP vision is to have an integrated network of cameras, weigh-in motion sensors and strategically located safety centres covering New Zealand. This enables intelligence-led regulation at scale, targeted intervention with non-compliant operators, and safe interception and risk screening of heavy vehicles by New Zealand Police.
“We’re aiming for every heavy vehicle paying its fair share, improved heavy vehicle safety, efficient and effective regulation, and a reduction in pavement damage.”
Currently, the Glasnevin and Paengaroa sites have recieved this updated technology and are operational. Sites at Rakaia (south and north) and Stanley Street will come online next year, Ohakea in early 2025, and Mackays, Taupo and Bombay in 2026.
He said that in addition to weight, RUC and permit checks, enhanced screening for non-compliance extended to CoFs, regos, green/pink stickers and unconfirmed owner/ stolen vehicles.
“This adds a lot more capability to screening, and for non-compliance, we can pull off trucks from the road. Data is captured 24/7 and stored in a centralised database, and if a vehicle fails a screening and the site is open, it will be pulled in.
“In the future, we’ll look at the potential to include worktime breach detection, too,” he warned.
Bridge said that a heavy vehicle was screened every nine seconds at Glasnevin and Paengaroa. Between them, the CVSP had thus far saved tens of thousands of hours for compliant operators and realised financial benefits of about $5 million to date.
“We’re building a profile on the industry’s trucks and operators. Infrastructure and weight are important, but the programme is much more. We’re trying to build a system based on data and insight. Intelligence will change how we work,” Bridge concluded.
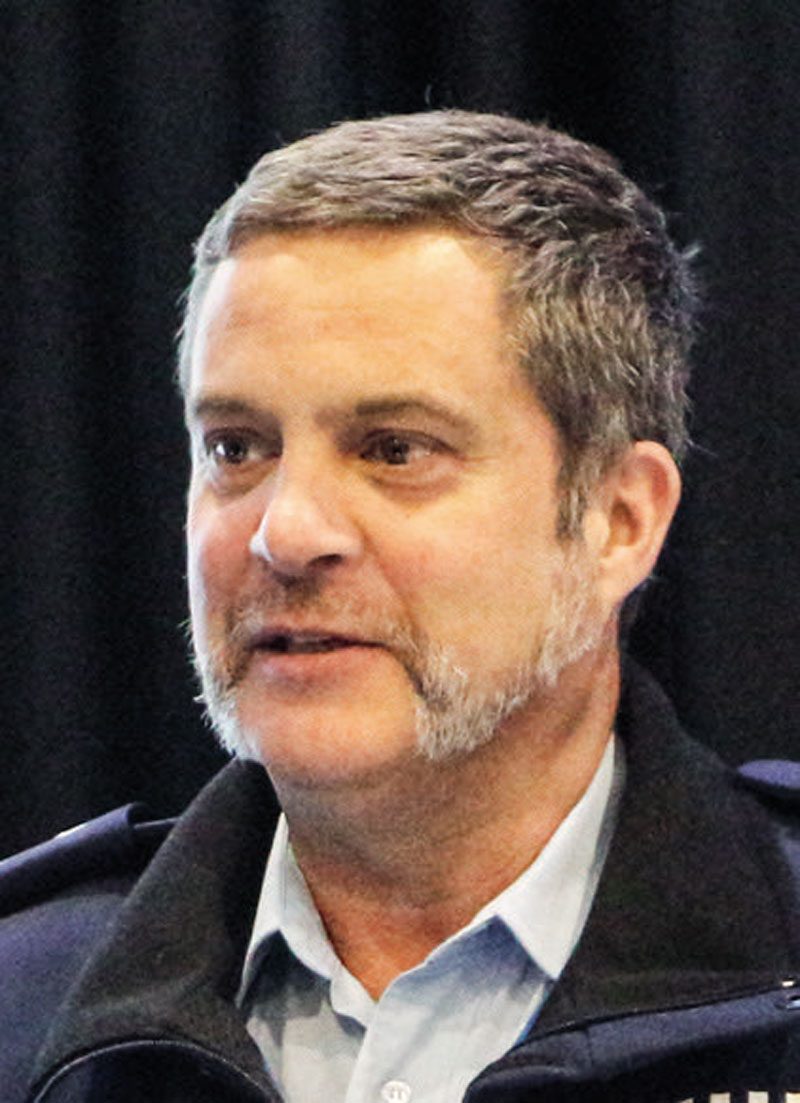
Finally, inspector Scott Richardson, national deployment manager, CVST, discussed the impact of new technology on heavy vehicle road policing. He said part of the CVST’s strategic reset was to refine its focus.
“Crashes and death and serious injury (DSI) crashes among heavy motor vehicles are heading in the right direction. There were less than 2500 HMV crashes in 2022, which is less than the previous low in 1989. There were just over 250 HMV DSI crashes in 2022, an overall downward trend from over 420 in 1990, but not at the low of just over 200 in 2010. In more than half of fatal crashes, the HMV driver is not at fault.
“We’re doing well as a nation, but still behind Australia and Europe. A lot of it is due to the infrastructure, drinking and driving, and distraction.”
Richardson said the new commercial vehicle safety centres would dramatically change how the police operated and would come with a dramatic increase in staffing.
“We know a 20% increase in inspection results in a 4% to 6% reduction in accidents. We know there is a relationship, and we’re doing the right work.
“We’ve set a target of 50,000 commercial vehicle inspections a year, from low-level standard inspections to brake machine and pit inspections. There were 59,280 inspections last year, but most were low-level. The new systems will enable flagging of trucks, so officers don’t waste anyone’s time – in 2022, 84.7% of vehicles inspected required no action. The percentage of trucks not allowed to leave the centres after inspection is actually quite low.”
Richardson said there was a push to focus speed enforcement on 100km/h areas, the CVST’s mobile brake roller testers would soon come online, and there would be greater use of thermal imaging cameras. He also said the police followed up on any dashcam footage shared with the CVST, and he encouraged this.
In conclusion, Richardson said: “We are working with Waka Kotahi to identify how to best approach companies that have issues. There will be no surprises [for these operators]. We want an industry that puts safety at its centre. We know we can’t be everywhere at once and that we can’t arrest and ticket our way out of problems.”
Read more
IRTENZ Conference 2023 – PBS
0 Comments12 Minutes
IRTENZ Conference 2023
0 Comments12 Minutes