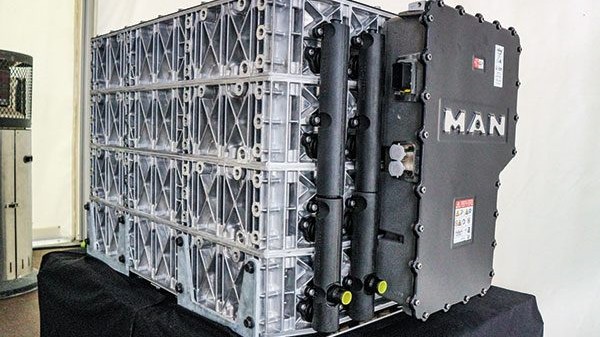
As electric drives rise in capability, one key to their ultimate success will be matching an increasing demand for batteries with supply. MAN appears to have that well in hand.
It seemed to generate far more than the current required to thrust an eTruck down the road. I found its mere form factor intriguing. It looked like an alien interstellar vehicle, and I felt like one of the more primitive characters from Arthur C Clark’s 2001: A Space Odyssey, obsessed with the monolith before me. Thankfully, though, it had MAN proudly stamped on the black plastic shroud at the front, which reassured me its origins were rooted among these fine folk of earthly origins surrounding me.
Nuremberg in Germany’s Bavaria region is the long- standing home to MAN’s engine operations. The city’s ongoing role as the Lion’s ‘powerhouse’ looks assured with the announcement mid-last year that MAN will invest €100 million over the next half-decade in battery- manufacturing operations.
As you’d expect in 2023, the approach to the project looks a lot different to what we would have seen even half a century ago, with environment, health and safety, use of technology, and collaboration key pillars right from the initiation of the R&D and discovery process.
Beyond MAN’s own sense of social licence, there’s good reason to ensure all the new-era commercial boxes are ticked, with the Bavarian state government stumping up €30 million for energy research and technology funding between 2023 and 2027, providing funding and budgetary requirements are met. The funds will be used for research into battery assembly, cell chemistry research, battery safety and recycling.
Once up and running at full capacity, the new plant will produce 100,000 battery packs a year – enough for 18,000 to 20,000 trucks and buses – and it will employ 350 people.
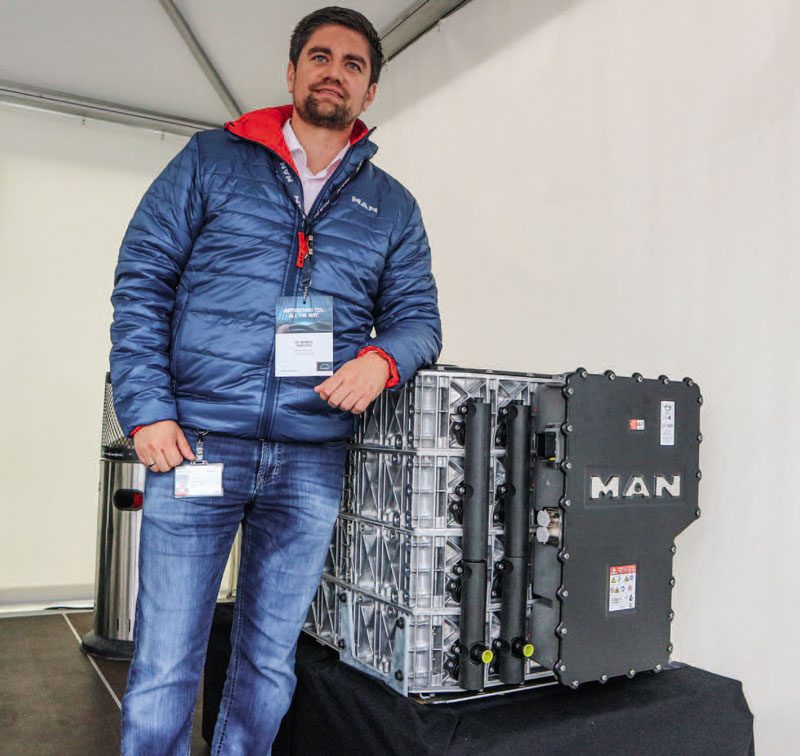
Not all batteries are created equal
The increased focus on horses for courses heralded by the electric propulsion era goes all the way to the energy source itself. While there’s immense resident IP in electric propulsion within MAN’s parent Traton Group, trucks are not cars. As such, there has been significant R&D into the continued evolution of the truck solutions within MAN itself.
“Commercial batteries are driven many more kilometres under very different circumstances,” says Dr Markus Pröpster, the man in charge of the Nuremberg battery project. “A private car might recharge twice a week, whereas a truck may need recharging twice a day, with the truck recharges likely to be fast, high-capacity events, not traditionally great for battery life. This is why we’ve developed specific chemistry for the trucks and buses, allowing retention of service life. We have tapped into expertise from within the wider group’s other brands, including our colleagues at Scania, as well as externally, from universities.”
While archrival Daimler heads down the lithium iron phosphate road for its HV battery technology, MAN’s thrust will come from lithium- ion units with an NMC (nickel, magnesium, cobalt oxide) cathode due to a higher energy density that makes this technology possible. The benefits for this cathode construction are excellent specific energy, low self- heating rate, and robustness where frequent cycling occurs, e.g. automotive and energy storage.
“As we see with things like our phone, the market is very dynamic with huge step changes coming every three to five years,” says Pröpster. “Think of the phone you had five years ago to the one you have today. Likewise, electric propulsion. Our batteries already have a high level of maturity. These will be generation three for us; the first went into the eTGM in 2018, the second into the Lion’s City E buses and now generation three in our buses and eTruck. We have invested heavily in developing IP in-house rather than a totally outsourced model. It allows us to retain a core competency at a time when change comes quickly.”
The individual cells will be sourced from a European- based supplier also used by the Volkswagen Group.
Blocks with a brain
“It has been so important to have R&D and production work together on this project, so we have close cooperation and communication, ensuring the best outcomes for quality, production efficiency, and cost.”
The result of all that intracompany collaboration and key to the goals set at the start is modulation.
The batteries Nuremberg will produce take the modular theme to the nth degree with a modular, within modular, within modular approach – almost electric Lego. It is what gives them the symmetrical alien-craft-type form factor.
Although they come in both oblong (buses) and classic cube (truck) forms, the architecture is the same. A metal frame supports modular cells stacked in layers, with each layer having its own temperature control plate at the bottom. The layers are then connected to low- and high-voltage wiring, and then the controller resident behind that black MAN monogrammed box at the front.
“It’s a key difference between the pas-cars [passenger] and commercial,” says Pröpster. “The pas-cars are single-layer batteries; ours are multi.”
The controller oversees the output and, in conjunction with the truck’s onboard systems, manages temperature. “The rule of thumb is if you’re feeling good, then so is the battery. About 10° to 30° is what they like.”
Because batteries come with a weight penalty, there’s zero point in having more than you need. A linehaul eTruck will house between four and six of the units. (Refer New Zealand Trucking magazine, Dec 22/Jan 23, One Giant Leap for MANkind.)
As we all know, time is money when it comes to trucking, and the commercial batteries are designed with both slow and fast megawatt charging in mind – able to take a fair old dose at 700kW.
Safety is a key parameter, as it is with any automotive component. The battery modules are subjected to all manner of impact and water- ingress testing. Every line- produced battery module will have to pass a 25-parameter test before release.
Likewise, there’s been a huge emphasis placed on the battery modules’ end-of-life journey. The intention is for a second and third use in less demanding transport tasks as well as stationary placements. Their modular nature means mid-life replacement of components as needed is also feasible. Like everything, though, there is a finality, and in that MAN has aimed for a 97% recovery and reuse rate for all components.
Deck the halls
“In the R&D phase, staff are dressed in safety clothes that would not be practical in a high-volume line-production environment,” says Pröpster. “Hence, the R&D team and production teams have worked closely throughout. Production staff are also being trained to assemble the batteries safely.”
Until the last quarter of 2022, the battery modules produced were deemed prototypes and assembled by the R&D team. That’s now progressed to a small serial production line producing about 2000 to 2500 units per annum, which will accommodate demand as it ramps up toward 2024 and the arrival of the eTruck to market. The end production environment will look very different from R&D assembly and current low-volume series production with refined production processes and automation, all resulting from that close collaborative effort.
“We are undertaking extensive levels of training to bring our people in the factory, and those in aftersales and service on the journey, transitioning from diesel trucks and engines to electric. The plant will create 350 jobs.”
Building of the final production hall commences in Q3 this year and will be ready for occupancy in Q3 next year. Full-blown assembly won’t come online until 2025, with target numbers of about 100,000 units each year. “That will grow quickly between 2025 and 2030,” says Pröpster.
Not surprisingly, looking a little farther down the road, that production increase also implicates Traton Group’s other European heavy-truck marque, Scania.
“The factory is planned to be flexible and able to integrate production of Scania batteries also, even though now the batteries are not 100% the same due to the different frames on the respective 2024 and 25 models. In the future, when looking at common products, common battery production is planned,” explained Pröpster.
Next month: The charge ahead!
Read more
Road to Zero Isuzu styles
0 Comments6 Minutes
Ready for the harvest
0 Comments12 Minutes
Super Swede
0 Comments11 Minutes
VGA introduces electric
0 Comments8 Minutes